While promising faster builds, modular housing faces roadblocks
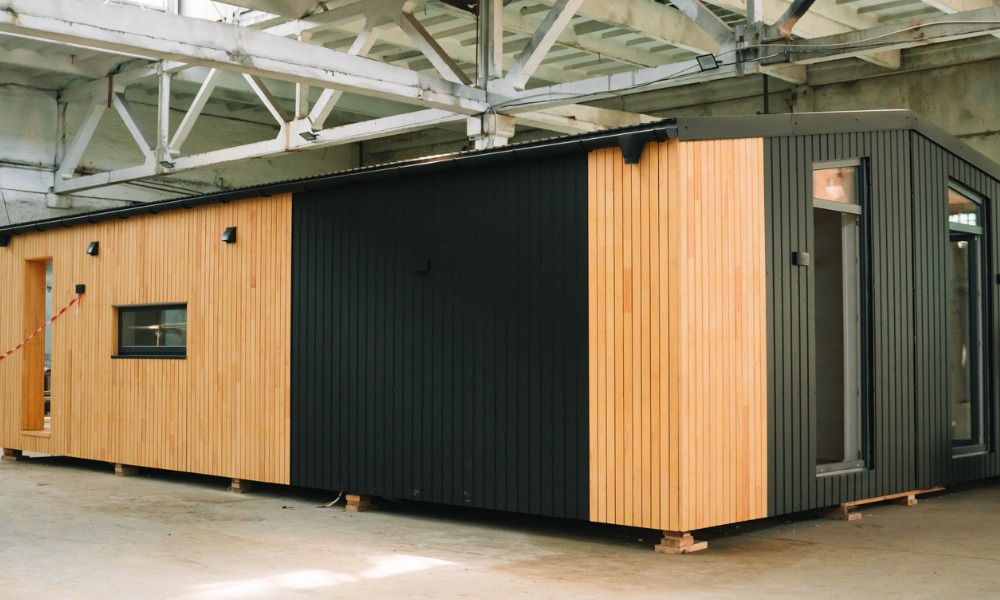
The federal government is promoting modular construction as a solution to Canada’s pressing housing shortage. However, industry insiders warn of several roadblocks hindering its widespread adoption.
Prime Minister Justin Trudeau has advocated for modular housing, which is assembled in a factory and then installed on-site, unlike traditional construction. This process can speed up construction by up to 50%, reduce waste, and potentially lower costs by up to 20%, according to a McKinsey report.
“When I talk about making it faster to build homes, modular housing is a big part of it,” Trudeau said in a July statement.
To encourage adoption, the government has pledged $500 million in loans for apartment builders using modular construction and other innovative techniques, along with funding for local innovative housing solutions and efforts to reduce regulatory barriers.
However, industry experts said that several significant roadblocks need to be addressed for modular construction to gain traction.
Industry hurdles
Canadian Home Builders’ Association CEO Kevin Lee pointed to regulatory delays, development charges, and mortgage rules as significant barriers.
“It is not as simple as, ‘Oh, well, somebody just thought of modular housing, so let’s do it,’” Lee told the Canadian Press. “There are a lot of barriers, there’s a lot of risk, and that’s why we need all of these systemic changes to make sure that the investment pays off.”
The challenges faced by modular construction companies highlight these roadblocks.
Z Modular recently closed its Kitchener, Ontario factory despite being the first to secure insurance from Canada’s housing agency for a modular apartment build.
Barry Zekelman, CEO of Z Modular’s parent company, cited “inefficiencies in financing, rising costs and regulatory delays” as reasons for the closure.
“Despite an obvious housing crisis, Canada has lacked the foresight to enact the changes necessary to encourage investment and enable developers to be successful,” Zekelman previously said. “Unfortunately, despite our investment of tens of millions of dollars, our teammates have become the victim of the tragic reality of a broken system.”
The modular construction sector faces high initial costs and requires steady demand to cover these expenses, making it vulnerable to the cyclical nature of Canada’s housing market.
“Because of the boom-bust cycle, it’s really tough to make those investments ... if you have that big overhead, instead of just slowing down, it can make you go bankrupt,” Lee explained.
This issue has led to several notable failures in the industry, including the collapse of Nomodic Modular Structures Inc. and Nexii Building Solutions.
Success stories
Still, some companies have found success in modular building.
Bird Construction Inc., which entered the modular market in 2017, recently secured a contract to build Canada’s tallest modular project—a 14-story apartment building in Vancouver for B.C.’s housing agency.
“Modular construction is gaining considerable momentum in North America,” Bird CEO Teri McKibbon said in a statement at the time.
Alberta-based Northgate Industries Ltd., which has been in the modular business for over 50 years, has diversified its offerings to include remote work camps and rural hospitals.
Read next: PEI government calls for modular housing facility proposals
Director Ali Salman noted that while there is growing demand from government-led projects, the private sector remains hesitant unless faced with high labour costs or remote locations.
Salman pointed out that the biggest hurdle is still the lack of consistent demand, advocating for government support similar to what has been provided to the automotive and oil and gas industries.
In countries like Scandinavia, where modular construction accounts for nearly half of the housing stock, government support has been crucial. However, in Canada, the fragmented construction sector poses additional challenges.
Steven Beites, a professor at Laurentian University’s McEwen School of Architecture, emphasized the need for increased awareness and education about the benefits of modular and prefabricated building methods.
“It’s really about educating and sharing that knowledge,” Beites said, advocating for a shift away from traditional “stick-frame” homes towards more efficient and sustainable construction techniques.
Make sure to get all the latest news to your inbox on Canada’s mortgage and housing markets by signing up for our free daily newsletter here.