COVID-19 has had an unexpectedly severe impact on lumber prices
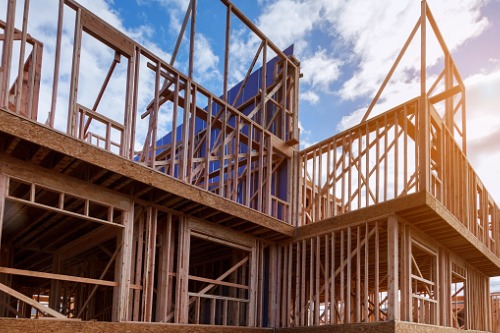
When COVID-19 first started disrupting Canadian businesses in March, the real estate sector was expected to come to a screeching halt. No one would be buying, no one would be lending, no one would be building. For better or worse, not a single one of those predictions has come true. While lenders, realtors, mortgage brokers and sellers have been thrilled by the unexpected turn of events, builders and buyers of new product have had to sit back and watch as lumber prices shot through the roof.
“COVID has impacted operating capacity and efficiencies across the supply chain, from logging operations, mills and transportation systems to suppliers and retailers,” says Canadian Home Builders’ Association CEO Kevin Lee. “Public health requirements and persistent labour shortages continue to impact operations at a time when the industry is trying to catch up.”
With lumber mills shuttered, construction being deemed an essential service and Canadians shut-up inside their homes engaging in a heroic amount of renovation activity, the result has been a supply-demand imbalance, and price escalation, never before seen in the North American lumber space.
“We’ve had in the range of a doubling of lumber prices,” since the beginning of the pandemic, says Residential Construction Council of Ontario president Richard Lyall.
At the outset of the pandemic, Lyall explains, Canada’s lumber mills were operating under what seemed like safe assumptions – that a halt in construction would slow demand and that COVID-19 would be a relatively short-term problem to contend with. A brief decrease in production, it was presumed, would be offset by an even more pronounced drop in demand. But the drop in supply that kicked off as Quebec closed some of the country’s most important mills was the only part of the equation to materialize. Construction, in both Canada and the U.S., where softwood lumber tariffs have done nothing to quell the country’s appetite for Canadian lumber, has continued unabated.
“We’ve done very well both in Canada and the United States,” Lyall says. “Homebuilding and high-rise condominium construction have been quite robust – quite a powerhouse in the recovery.”
Impact on home prices
In March, the composite price of softwood lumber was a shade under USD $400 per thousand board feet (mbf). In August, it was $900/mbf. But Lyall says the increase in price won’t impact all builders equally. Those with long-term contracts with suppliers have likely been able to avoid paying higher prices, while developers who sold their units before the pandemic will have to eat the increase costs. It’s the builders working on-spec, on smaller developments, or in more remote areas where prices are lower who may find themselves cutting some painful cheques and passing the increased costs on to buyers.
According to Lee, one lumber supplier in Saskatoon, Saskatchewan is currently quoting $1,200 per thousand board feet of lumber, up from $425 three months earlier – an increase of 167 percent. Floor sheeting is $50 per sheet, up from $17 three months earlier, while OSB sheathing for roofs and walls is $30 per sheet, up from $10 three months ago.
“This is increasing the cost to build a typical single-family house by $10,000 or more, and these prices have or will be passed to consumers as supply contracts expire,” he says.
Lee and the CHBA say there is more at stake than just higher home prices. Builders are already pulling residential lots off the market because of an inability to confidently price construction for homes that are still years away from being completed, meaning a potential drop in construction jobs that could create “headwinds not only for housing but for Canada’s long-term recovery trajectory.”
How long will prices stay elevated?
Lyall feels the pressure being put on lumber prices will soon taper off. Peak reno season has passed, which should mean a significant decrease in demand from homeowners. Mill production, though still far from normalized, has increased. The winter lumber harvest is expected to proceed, leading to a healthy supply of softwood next year – knock on wood.
“I expect it will get sorted out in due course,” he says.
If recent trends continue, if might not be long before Lyall is proven right. For the week of September 11, only seven of the 15 indexes tracked by Madison’s Lumber Reporter experienced a week-over-week price increase. It was the first time in months softwood lumber prices either remained flat or dropped.
To hasten the correction of the supply-demand imbalance, Lee says the CHBA is calling for federal leaders to work with domestic lumber producers to accelerate the ramp up of production, support a back-to-work transition for workers, and consider other ways to offset material shortages and rising construction costs.
“Given the housing supply shortage that continues to place upward pressure on home prices, it will be important to ensure material shortages don’t exacerbate the problem,” Lee says. “While housing starts are rebounding well right now, it is housing completions that ensure we add more supply, and those are currently at risk of being further delayed.”