Supply bottlenecks and unclear trade compliance rules stall construction timelines
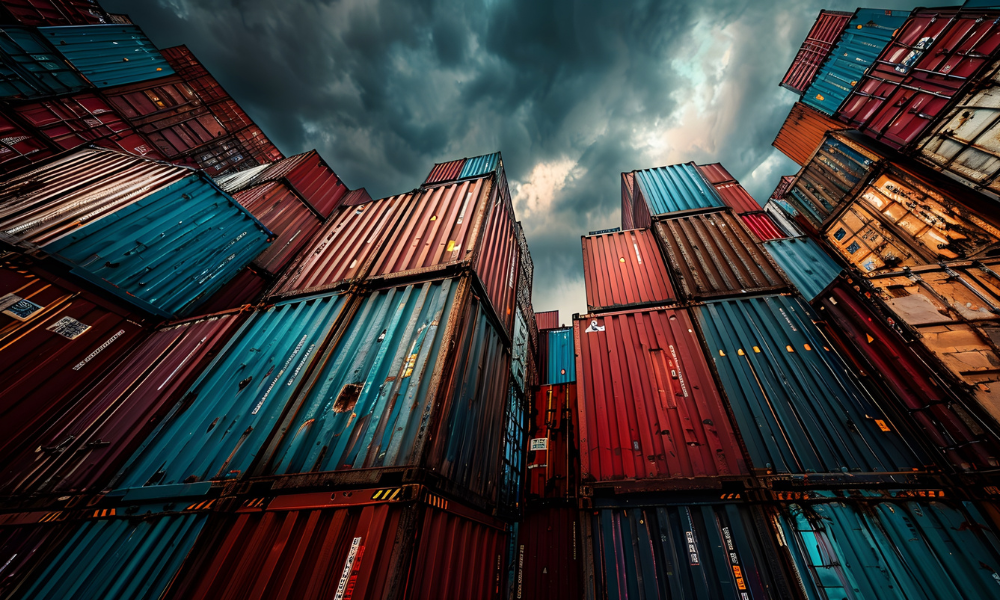
Tariffs on construction materials are adding complex layers of cost and delay to office building projects, creating a cascading impact across labour negotiations, product sourcing, and project timelines, according to new insights from Avison Young.
The firm’s analysis highlights how tariffs, particularly those involving aluminum, steel, and AV components, are inflating construction budgets and disrupting supply chains, especially for mid- to high-end office interiors.
Office improvement costs now vary significantly depending on design and technology needs. Arlene Dedier, principal and managing director of project management services at Avison Young said mid-range office spaces typically cost around $150 per square foot, while high-end spaces, such as those used by professional services firms, often exceed $200 per square foot.
Dedier also noted that basic setups of furniture range from $25 to $35 per square foot, mid-range setups from $35 to $50, and high-end configurations can go beyond $50 per square foot, driven more by the quantity and complexity of installations than by regional price differences.
Behind these rising costs is what Dedier called a "butterfly effect," where a tariff applied to US-made goods ripples into Canadian supply chains, influencing not just direct imports but also Canadian-made products that rely on American components. Tariffs on goods from China are adding another layer of complexity, prompting developers to consider sourcing materials from the EU or UK.
“We look to EU and UK manufacturers as alternatives to the US, which has a logistical impact,” Dedier said in an interview. “We can find Canadian companies for a lot of the products, but they're much smaller and will need to scale up. That is also part of the butterfly effect.”
The challenge, she said, is not just higher costs, such as a 25% spike in steel prices, but also confusion around how tariffs should be applied to materials already in transit.
“This is already having an impact as materials can't get released because people logistically don't know how to apply the tariffs,” Dedier explained.
“We must determine how to process that and to whom are the tariffs paid.”
Read next: Toronto's office-to-housing conversions 'generally not feasible,' says report
The mounting delays are leading real estate project managers to re-evaluate supplier relationships and procurement strategies to ensure compliance and avoid jeopardizing occupancy timelines.
“Like the domino effect we saw during the pandemic, the container is stalled in the port, and that container is scheduled to be in another port in three weeks. It is disrupting the supply chain,” Dedier added.
Make sure to get all the latest news to your inbox on Canada’s mortgage and housing markets by signing up for our free daily newsletter here.